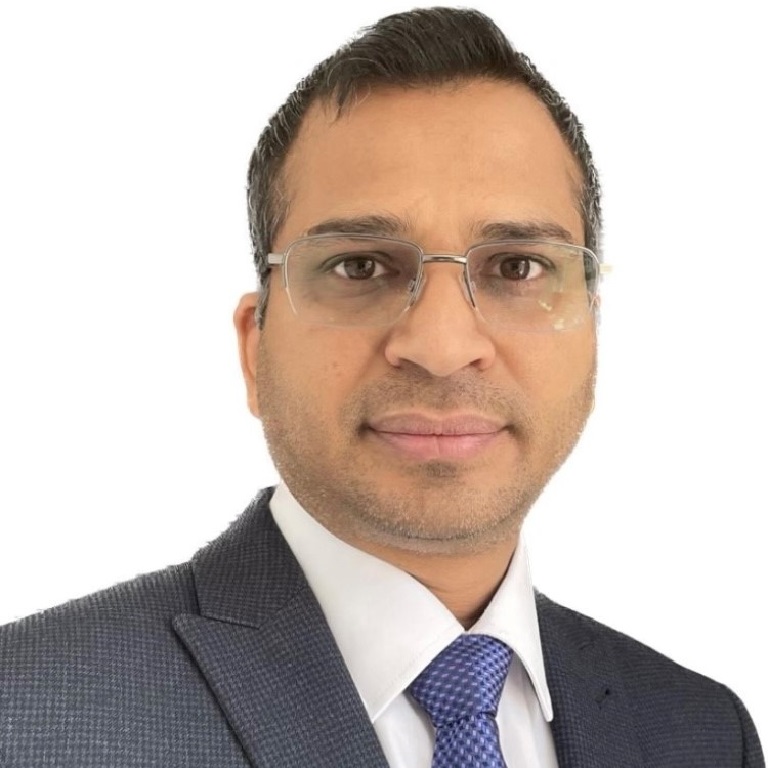
Sanjeev Lakhera
Vice President, Energy and power
-
United Kingdom
The conversion of plastic waste into fuel is now a reality, due to the innovations in applying the chemical processes of pyrolysis and gasification. Several local authorities in the UK have already granted planning permission for plastic conversion plants able to handle mixed, contaminated plastics and film that can’t be treated by traditional, mechanical recycling.
In the previous articles of this series, we outlined plastic-to-fuel technologies and their risks. In this final instalment, we explore how to mitigate those risks.
The selection of an appropriate site for a conversion plant is a key aspect of risk management. Only projects with detailed risk mitigation measures, robust remediation plans, and overall low-risk profiles are likely to be granted planning permission in the first place.
Process safety needs to be core to a plastics-to-fuel plant’s engineering and design.
The heat ranges used in plastic pyrolysis and gasification are much higher than those in traditional oil refineries, creating another layer of risk. For example, high temperatures lead to the creation of exotic materials. Their presence may necessitate a positive material identification (PMI) of the metals used in the reactor to assess the perils associated with them at elevated temperatures.
A plant needs to be well laid out, for example, with wide roads providing access for maintenance and emergency services. The control room should be blast proof and a safe distance from the reactor.
The safe and efficient running of a plastic-to-fuels plant is dependent on having the right operational, maintenance, and inspection systems in place. Plants must adhere to the codes and standards of the UK’s Health and Safety Executive. These include special work permits authorising hot and cold work, hot work with spark potential, working at height, and confined space entry, among other activities. In pyrolysis, nitrogen gas is used to create an inert atmosphere, which is effective in explosion prevention. Major hazards associated with the process of inerting include asphyxiation and loss of the inert atmosphere, which are both covered by HSE codes.
There should be detailed procedures for shift handovers, including the completion of logbooks detailing work carried out by the previous shift, the state of the process equipment, any known defects, and the status of fire extinguishing systems. Incident reporting of equipment breakdowns and loss of containment events needs to be a matter of course, and systems must be in place for facility maintenance. Staff should take induction courses, helping them to understand the inherent risks of the plant, and be qualified to an appropriate level to operate the site.
A major fire can occur in any plant where pyrolysis and gasification processes are taking place. Some of the largest insurance losses in the hydrocarbon industry have been at plants handling plastic products. Appropriate control and safety systems must be in place, including having fire and gas detection methods and procedures for safe plant shutdown in case of an emergency.
Preparedness includes having a fire pre-plan (a document containing essential information about the plant) covering a range of scenarios. These can contain, for instance, requirements for fire water and foam at the facility, location of hydrants, and plant layout. Scenarios should be evaluated regularly with tests incorporating unannounced drills. Leaks also have to be planned for, and measures for gas and fire retention put in place.
The risks associated with fuel-to-plastic plants are manifold, encompassing liability, environmental, construction, operational, property, directors and officers (D&O), and business interruption. An independent review of your plant and systems by an engineer will provide recommendations for high impact risk mitigation strategies. A pre-startup safety review (PSSR), for example, can be carried out to confirm that all appropriate elements of process safety management have been addressed satisfactorily, and that the facility is safe to start up.
These types of reviews help build bridges between risk engineers, insurers, and risk managers, and the client and the underwriter. Benchmarking systems can provide an opinion of the risk, assessed against peer plants.
For underwriters and brokers alike, supporting the development of plastic waste-to-fuel conversion aligns with the increased focus on environmental concerns and the desire to support clients with their transition to net zero.
If you have any questions about producing fuels from plastics, the associated risks, and how to mitigate them, please contact your Marsh adviser.
Vice President, Energy and power
United Kingdom
Client Executive, Energy & Power
United Kingdom
CEO, Energy and Power, Marsh Specialty
United Kingdom