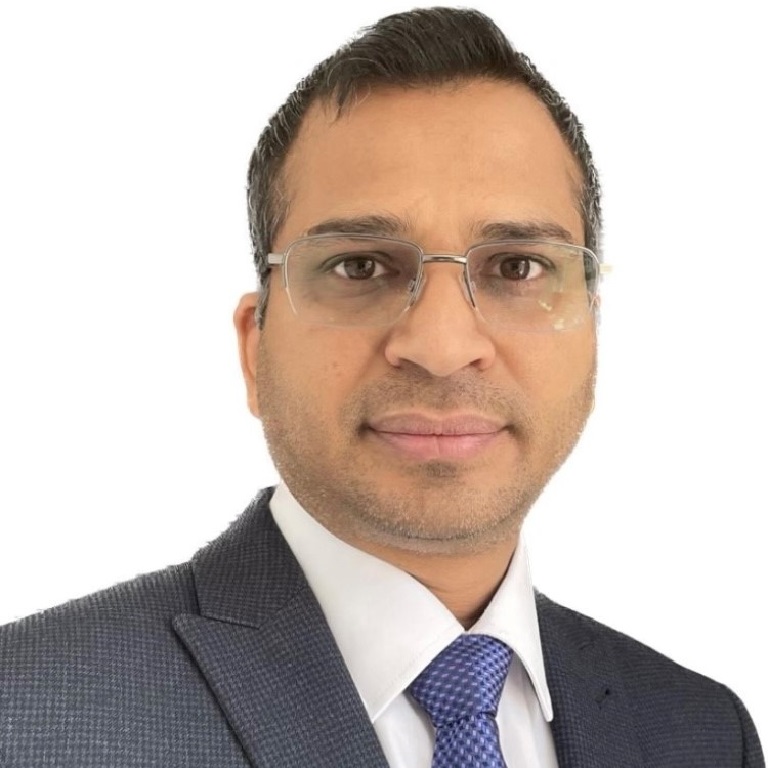
Sanjeev Lakhera
Vice President, Energy and power
-
United Kingdom
Plastic is part of our daily lives — it’s hard to imagine life without it. However, only 9% of plastic is recycled, with 12% incinerated and the remaining 79% landing in our oceans and landfills, where scientists predict it will take up to 450 years to biodegrade.
With the energy transition underway, the UK Government for the first time, in its upcoming Energy Bill, has enabled support of recycled carbon fuels, including those made from plastic waste. In this first instalment of a three-part series on plastic-to-fuel technology, we outline this new process and its challenges; future articles will examine the associated risks and how they can be mitigated.
There are several ways to recycle plastics, including:
Mechanical recycling: Plastic is crushed into granules that can then be used in another product, but its molecular structure is retained. This is a widely-used technique, but has limitations. For instance, sorting methods are not yet available at scale to differentiate food-grade plastics, which command higher prices. Plus, there are environmental health concerns relating to the release of particles during this process. Companies are currently repurposing plastics, using a variety of methods, into rugs, packaging, shoes, plastic jackets, skateboards, and construction materials.
Chemical recycling: There are currently two chemical processes for converting plastic waste to an energy carrier — pyrolysis and gasification (see figure 1). These methods break down plastic, remove any impurities, and convert it back to its chemical components. They have the potential to tackle the problem of plastic pollution while also providing an alternative source of energy.
Collection and sorting: Plastic waste is collected from sources such as households, industries, or recycling centres. It is sorted to remove any non-plastic materials, like paper or metal.
Shredding and pre-treatment: The sorted plastic waste is shredded into small pieces to increase the surface area and improve the efficiency of the subsequent processes. The shredded plastic may undergo pre-treatment processes — for example, washing or drying — to remove contaminants such as dirt or moisture.
Pyrolysis: The shredded plastic is subjected to high temperatures, typically in the range of 300°-500°C (572°-932°F), in an oxygen-free environment, a process known as pyrolysis. The plastic undergoes thermal decomposition and breaks down into simpler hydrocarbon molecules.
Vaporization and condensation: The vapors produced during pyrolysis are cooled, causing them to condense and form a liquid. This liquid consists of various hydrocarbon compounds, including impurities, which can be further refined to obtain usable fuels or chemical raw material components.
Refining: The condensed liquid is processed through further refining steps, such as fractional distillation and hydro-processing, to separate and purify the different hydrocarbon fractions. The resulting fuels can include gasoline, diesel, kerosene, or similar products.
By-product handling: Some by-products may also be generated during the process, such as char or residue. These may undergo additional treatment such as hydro-cracking, or be recycled or disposed of appropriately.
Gasification: In gasification, plastic waste reacts with a gasifying agent — such as steam, oxygen, or air — at high temperatures between 500°–1300 °C. This process produces synthesis gas, or syngas, that can be used to produce fuel for cells that can generate electricity.
One advantage of gasification compared to pyrolysis is the greater flexibility to jointly increase the value of plastics of different composition or mixtures or plastics mixed with other feedstock.
Source: American Chemical Society
The fundamental molecular components of plastics consist of hydrogen and carbon. Fuels produced from plastic waste can be tailored to meet a certain need, such as fuel for industrial, aeroplane, ship, locomotive, or diesel engines, and boilers. Plastics may also be processed to harvest hydrogen — a clean fuel that when consumed in a fuel cell, produces only water. As such, they are suitable substitutes for fossil fuels.
There is much excitement about this relatively new technology worldwide — with visions that landfills could become the oil fields of the future. Several councils in the UK have already granted planning permission for plants that will convert plastic waste into fuels (see box), with other local authorities expected to follow suit. As well as in the UK, from India to Australia, plastic-to-fuel projects are underway. The benefits of creating fuel by using this technology include:
Source: National Packaging Waste Database (2020)
There are a number of environmental and health considerations associated with the chemical recycling of plastics due to the release of nitrous oxides, sulphur dioxides, particulate matter, and other harmful pollutants. Oil from plastic waste has more than a 20% lower flash point in comparison to regular diesel at under 40°C, increasing the opportunity of spontaneous ignition. The feedstock is variable (the raw products used in plastics, for example, vary from country to country). The different polymers that are fed into a pyrolysis reactor break along different patterns, which can pose challenges. In particular, molecules with high degrees of branching crack more easily than linear ones, which makes process control and reactor stabilization more difficult.
Once a plastic waste-to-fuel recycling plant is built, its costs of operation are comparatively low, but setting up the new unit can be costly. Lack of incentives and proper systems for waste collection can hinder the availability of waste plastic feedstock.
Additionally, the recycling industry is concerned that plastic waste-to-fuel will undermine the economy of other waste-to-fuel processes, such as solid waste-to-fuel. There is also the argument that the use of waste-to-fuel programmes does not resolve the issue of over reliance on plastics, but just increases their usefulness for the same amount of environmental impact.
The plastic recycling industry, however, is continuously evolving, and new technologies and innovations are being explored to improve the efficiency and sustainability of plastic-to-oil processes and enhance the quality of the end product.
Future articles in the series will explore the risks associated with plastic fuels and ways to mitigate them.
Vice President, Energy and power
United Kingdom
CEO, Energy and Power, Marsh Specialty
United Kingdom
Andrew Herring assumed the role of CEO of the Energy and Power Practice for Marsh in the UK in 2013. He has had an extensive career as an insurance broker in a number of different organisations, but always based in the UK, and always dedicated to the energy and power sectors.