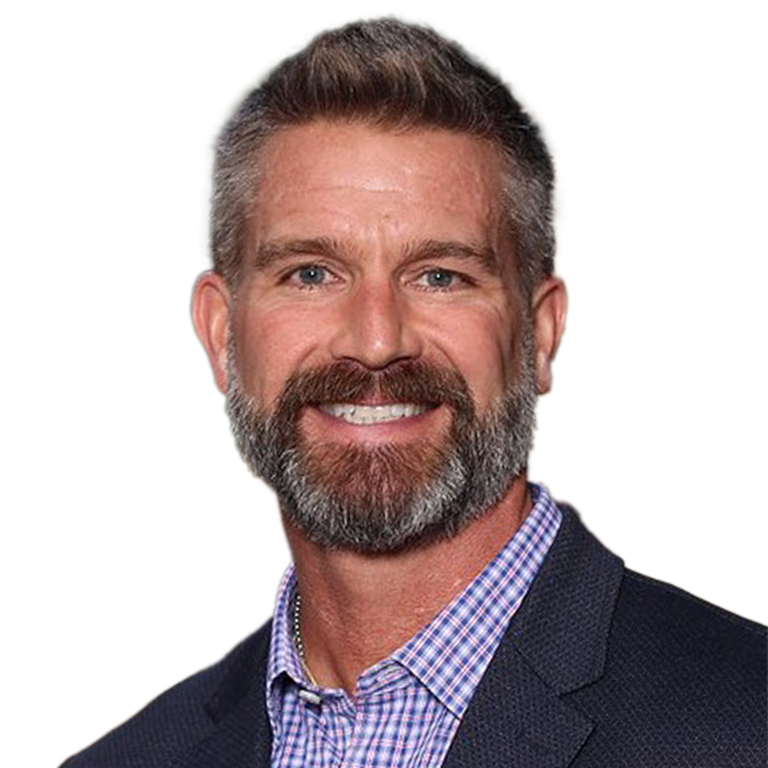
By David Carlson ,
Manufacturing and Automotive Practice Leader, US
10/29/2021 · 5 minute read
Controlling costs has always been a key goal for businesses, but it’s arguably never been more important than it is today. After nearly two years of pandemic-related challenges and with new ones emerging — including inflation — cost reduction efforts now sit at the top of many corporate boards’ and C-suites’ agendas. And for many manufacturing and automotive companies, those efforts include a focus on their cost of risk — notably, for workers’ compensation.
Calculating an organization’s risk costs — whether in total or for specific areas — is hardly a new idea. In fact, the insurance and risk management community has been doing just that for decades to guide decision-making and prioritization.
But ask a dozen industry professionals how to calculate those risk costs and you are likely to receive a dozen distinct responses. One commonly used methodology is to add up a company’s insurance premiums, retained losses, and risk management administrative expenses.
Another way to look at it is the sum total of all costs affected by the risk management function — including not only insurance expenses, but costs related to quality control, absenteeism, and more. And it’s a mix of both variable and fixed costs.
No matter the precise method you’re using, quantifying your cost of risk can enable you to arrive at a directionally accurate valuation of your organization’s major risk areas. That can help drive smarter, more holistic risk management decision-making, and the calculation of a more consistent and reliable metric that is easily understood by risk professionals and financial executives alike.
Although every company’s circumstances are unique, variable costs typically make up about 75% of their overall cost of risk. The factors behind those variable costs are constantly changing — cyber, for example, has emerged as a greater cost driver for many organizations over the last 18 months.
Product liability costs are also rising. That’s due to a combination of mounting litigation costs — fueled in part by what the insurance industry refers to as “social inflation” — and more sophisticated engineering, which has resulted in highly complex technologies being embedded in any number of consumer products that are manufactured and sold today.
But for manufacturing and automotive companies, the biggest source of these variable costs is usually casualty — specifically, workers’ compensation. According to the Occupational Safety and Health Administration (OSHA), manufacturing and automotive companies have made great strides to reduce the frequency of workplace injuries over the last decade (see Figure 1). But even those lower frequency rates continue to challenge employers.
So does severity: According to Marsh data, manufacturers incurred nearly $16,000 per workers’ compensation claim through the first three quarters of 2021, and nearly half of the cost for lost-time claims was generated by medical expenses, which have more than doubled for all employers over the last two decades, according to the National Council on Compensation Insurance.
Although some companies have a solid handle on their workers’ compensation cost of risk, others have had trouble getting started. The first step to managing this risk is to quantify it — as the saying goes, you can only manage what you measure and you measure what you value.
It’s important that employers look for the right data and gather it from the right places. Data on broad industry trends can come from several sources, including:
To take appropriate and effective action to reduce the cost of injuries, employers must also make sure they have the right information — for example, the most common and costly injury types. They can then complement insights from these sources with organization-specific metrics, which can be developed internally and in conjunction with their insurance and claims advisors.
For example, it is useful for manufacturers to know that according to data compiled by Marsh via our Blue(i) Claims platform, the leading causes of workers’ compensation losses for the industry through the first nine months of 2021 overall were strains, slips and falls, and being struck by other objects. Additional tools — such as Marsh’s Safety Performance Ind — can help you hone in on your organization’s strengths and weaknesses and identify its unique cost drivers.
These and other data types can inform a number of actions by employers to reduce costs, both before and after losses. But the greatest promise for employers lies in injury prevention. Employers can address potential problems before they grow out of control by coupling claims data, incidence rates, and other trailing metrics with leading indicators, such as near-misses.
A well-known concept in environmental, health, and safety circles is Heinrich’s triangle, which posits that a certain number of near-misses — workplace incidents with no injuries — will lead to a certain number of incidents with injuries; while many of these will be minor, a subset of them will invariably be more serious, and a smaller number will result in more severe consequences, including fatalities.
That means employers can prevent more serious occupational injuries and fatalities through early intervention to prevent or limit unsafe behaviors and near-misses. For example, a manufacturing or automotive company can track the number of near-misses — say, every instance of a pallet of boxes discovered on the floor of a racking area from an obvious fall, even ones that did not result in injuries, is a leading indicator that forklift training or pallet storage may need to be reevaluated.
Each of those instances can present opportunities for action, such as reinforcing safety training, changing processes and procedures, and more — all of which can ultimately contribute to a reduction of workers’ compensation cost of risk.